Basics of Reliable Wire Harness Production
Most of industries that require electronic equipment uses wire harness to keep different electrical wires safely on indoor and outdoor settings. Before the installation of wire harness within an electronic equipment, it has to satisfy use-case based requirements to avoid any damage either during the production line or at the field. Here, we cover some of best-practices and procedures that should be followed on cable assembly production to avoid such problems.
Sampling Procedure
To avoid any integration incompatabilities on production, a wire harness supplier and purchaser sides have to agree on a sample product and related technical drawing within a written -and signed by both parties, report that covers the information of used materials (such as terminal types, cable types and accessories), cable lengths, dismantle lengths etc. Consequently, it's better for both sides to keep replicas of this samples that had used on agreement to construct a common base on the product in between both sides.
Crimping Basics and Pull Test
Crimping is basically an integration of a terminal within wire. This operation can either be done within hand-tools (usually for sampling procedures) or machinery. Main crucial points to be considered are: Compatibility of cable within terminal, compatibility of crimping equipment within terminal and continuous testing / maintenance of crimping equipment. An improper crimping operation may lead a break off of cable within terminal (due to damage by excessive force on crimping) or conductivity loss (due to oxidation in between copper strands).
Below, we show how good crimp and unacceptable crimp is from different angles.
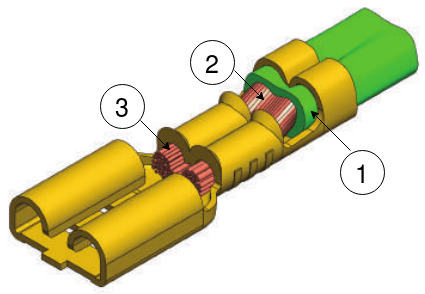
Good Crimp: Insulation presents at point 1, conductor presents at point 2 and 3.
To avoid such unacceptable crimps on wire harness production, pull test has to be periodically done (and recorded by) with a dedicated machinery. Besides, a visual test should be obtained on form of crimping material and formation of strands.
Electrical Testing
Generally, a wire harness has more than one branches -or ends- that may go off in a number of directions with several terminations on each branch. Here, a custom electrical testing for the specific harness has to be established and run to catch short connections or mis-wirings.
Hipot Testing
Hipot (High Potential) testing is a methodology to find insulation
problems that low voltage testing can not. A damaged insulation or
shielding may introduce a short connection (due to the relation in
between magnetic fields and current in between conducted materials) even
on non-conducting wires by high voltage. To avoid such cases on wire
harness integration, a wire harness manufacturer should emulate the
situation by same voltage level on harness with Hipot Testing equipment.